Session Track
November 03 (Friday)
마이크로/나노공학부문 포스터
Poster,
3층 로비,
09:50~10:40
- 옥종걸(서울과기대), 장원석(기계연), 강현욱(전남대), 심형철(기계연)
Fr16A-21
09:50~10:40
미세 유체 PDMS 몰드 조립체를 이용한 광경화성 고분자 기반 원자 현미경 캔틸레버의 고속 배치 제작
This paper reports rapid batch fabrication of atomic force microscope (AFM) cantilevers with photocurable polymers using microfluidic polydimethylsiloxane (PDMS) mold assembly. One PDMS mold contains negative base structures and connection microfluidic channels, both of which are simultaneously replicated via single transfer from 250-um thick positive SU-8 (100) patterns on a 4-inch silicon wafer. The other PDMS mold contains negative tip and beam structures replicated via double transfer starting from another 4-inch silicon wafer which is anisotropically etched by potassium hydroxide (KOH) and then 15-um thick negative SU-8 (2015) patterned. After the prepared PDMS mold pair is aligned with a custom PDMS aligner, hydrogel or photocurable polymers that are routinely used in stereolithography-type 3D printers are injected by an electronic pressure regulator into the empty space in the mold assembly. After the mold is fully filled with the photocurable prepolymer, UV (365 nm, 28.8 mW/cm2) is exposed for 10 seconds. Then, the PDMS mold assembly is separated and the cured AFM cantilevers are mechanically detached by using a tweezer. In this way, 40 AFM cantilevers having average tip radius of ~200 nm are simultaneously fabricated. For optical-lever type AFM instruments, thin metal (Ti/Au : 40 nm/80 nm) is deposited selectively near the free end of each cantilever by using a shadow mask. Finally, each polymer cantilever is individualized by using a tweezer and used for AFM imaging.
Keywords : Batch fabrication (배치 제작), Microfluidic (미세유체), Mold assembly (몰드 조립체), Photocurable polymer (광경화성 고분자)
Paper : Fr16A-21.pdf
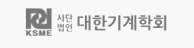
(사)대한기계학회, 서울시 강남구 테헤란로 7길 22 한국과학기술회관 신관 702호, Tel: (02)501-3646~3648, E-mail: ksme@ksme.or.kr