Session Track
November 02 (Thursday)
가스터빈 및 증기터빈
Oral,
제11발표장(304호),
08:40~09:40
- 방제성(KIMM)
Th11A-2
08:40~09:40
가스터빈 성능 및 신뢰성 향상을 위한 이차유로 및 냉각 시스템 설계
Improving gas turbine performance and reliability is very challenging target for most of the gas turbine designers. Secondary air system designer’s activities are involved in to increase pressure ratio of compressor and to increase turbine inlet temperature within structural limitations.
The main role of the secondary air system design is to provide all flow conditions in gas turbine system except primary flow path zone, such as cooling flow path, purge air flows in disk cavities and sealing flows in rotating and stationary parts. And also provide temperature conditions of whole gas turbine system at the all operating range.
For sub system level designing activities in gas turbine development. All sub components for secondary air system should built and validated within acceptable criteria to meet target performance.
In this paper, all kinds of secondary air system design works and results for 270MW class gas turbine power generation were described.
The main role of the secondary air system design is to provide all flow conditions in gas turbine system except primary flow path zone, such as cooling flow path, purge air flows in disk cavities and sealing flows in rotating and stationary parts. And also provide temperature conditions of whole gas turbine system at the all operating range.
For sub system level designing activities in gas turbine development. All sub components for secondary air system should built and validated within acceptable criteria to meet target performance.
In this paper, all kinds of secondary air system design works and results for 270MW class gas turbine power generation were described.
Keywords : 가스터빈(Gas Turbine), 이차유로 (Secondary Air System), 냉각 (Cooling), 프리스월 (Pre-Swirl), 씰(Seals)
Paper : Th11A-2.pdf
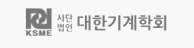
(사)대한기계학회, 서울시 강남구 테헤란로 7길 22 한국과학기술회관 신관 702호, Tel: (02)501-3646~3648, E-mail: ksme@ksme.or.kr