Session Track
November 03 (Friday)
기계요소/시스템/융합설계
Oral,
제13발표장(401B호),
13:00~14:00
- 채영호(중앙대)
Fr13D-3
13:00~14:00
항공기용 열교환기 매니폴드의 위상최적화 설계
The heat exchanger manifold of the aircraft serves to evenly distribute the fluid coming in through the inlet and then out to the heat transfer unit. To meet this requirement, the manifold must be designed to be lightweight and to withstand high internal pressures. Therefore, this study aims at minimizing the weight of the heat exchanger manifold through topology optimization.
To optimize the topology, the initial design space was first determined considering the inner surface of the existing manifold model with the outer surface shaped by a solid cube. A finite element model of the initial design space was created in ANSYS Workbench. Upper side of the manifold was then fixed to represent the welding joints of the manifold and an inner pressure of 5.5 MPa was applied on the inner surface of the manifold as boundary conditions. Six case studies were performed with different weight targets to obtain a minimized shape with maximum stiffness at a given volume, resulting in the key structure of the manifold being identified.
By observing the change in manifold structure due to weight reduction, we were able to select the key structure to distribute the load on the manifold. Currently, we further simply the shape of the topology optimised manifold reflecting the key structure identified in the case study results and we also plan to use the 3D metal printing process to manufacture the manifold optimised and simplified.
To optimize the topology, the initial design space was first determined considering the inner surface of the existing manifold model with the outer surface shaped by a solid cube. A finite element model of the initial design space was created in ANSYS Workbench. Upper side of the manifold was then fixed to represent the welding joints of the manifold and an inner pressure of 5.5 MPa was applied on the inner surface of the manifold as boundary conditions. Six case studies were performed with different weight targets to obtain a minimized shape with maximum stiffness at a given volume, resulting in the key structure of the manifold being identified.
By observing the change in manifold structure due to weight reduction, we were able to select the key structure to distribute the load on the manifold. Currently, we further simply the shape of the topology optimised manifold reflecting the key structure identified in the case study results and we also plan to use the 3D metal printing process to manufacture the manifold optimised and simplified.
Keywords : Topology Optimization(위상최적화), Hear Exchanger(열교환기), Weight Minimization(경량화), Stiffness Maximization(고강성)
Paper : Fr13D-3.pdf
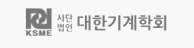
(사)대한기계학회, 서울시 강남구 테헤란로 7길 22 한국과학기술회관 신관 702호, Tel: (02)501-3646~3648, E-mail: ksme@ksme.or.kr